You can effectively electrify your fleet faster and at a lower cost by focusing on electrifying work functions along with miles driven
‘Fleet electrification’ is relevant across the transportation sector today, with reducing emissions and fossil fuel use both common fleet-wide goals. And while many focus on the environmental aspect, the truth is that there are sound business reasons to electrify your fleet; reduced costs and increased employee comfort and safety are two of the primary benefits.
While electric truck deployments by U.S. companies grew five times in 2023, the rollout of electric work trucks is moving slowly overall. This isn’t a huge surprise to those who have been paying attention. There are real challenges to the wholesale adoption of EVs, including concerns about vehicle range, limited availability of charging infrastructure and the need to integrate new vehicles into existing systems. COVID-related constraints, supply chain struggles and slow production schedules have also hampered the proliferation of EVs. Today, successful startups in the electric work truck space are still only filling orders in the low double digits.
As fleet managers look for viable electrification options, they understandably tend to focus on vehicles first. However, studies have shown that 53 percent of work trucks drive for less than four hours a day. The vast majority of a work truck’s life is spent lifting a bucket, digging a hole, mixing cement, or performing one of the other essential tasks that keep our world running smoothly. And just as EVs have made huge leaps in recent years, the electrified tools available for everyday tasks like lifting a bucket, digging a hole, or mixing cement have progressed tremendously.
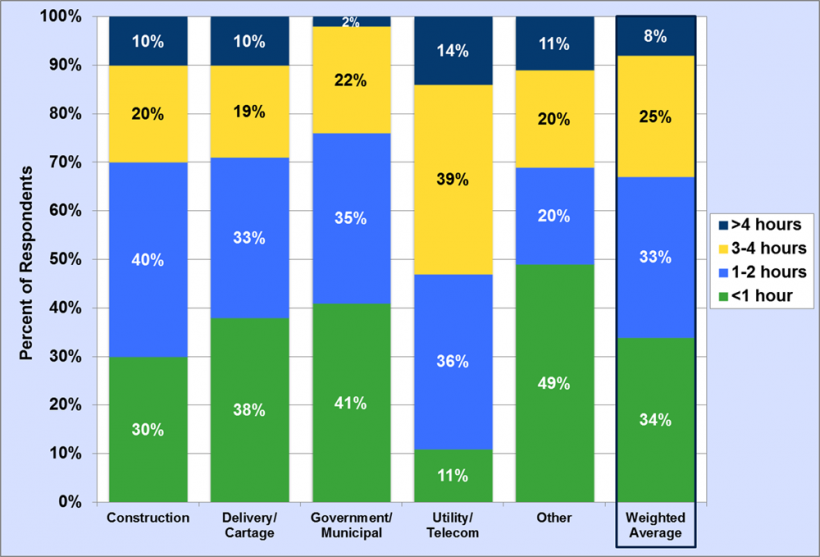
In other words, electrifying the equipment a fleet uses to perform its work can have a huge impact, even without electrifying the vehicles themselves. For utilities and other work-truck heavy fleets, that creates an opportunity. By electrifying work operations via new equipment, they can quickly and efficiently lower costs, meet emissions goals, and improve employee safety. That’s part of why approaching vehicles and equipment as distinct, but complementary elements of your fleet is essential to a well-balanced fleet electrification strategy.
Why Your Fleet Electrification Strategy Should Consider Vehicles AND Equipment
The traditional approach to fleet efficiency centers on improving fuel efficiency in the form of miles per gallon – or ‘driving efficiency.’ In other words, the best way to improve fleet efficiency is by buying more efficient vehicles. Based on this line of thinking, electric vehicles are the most efficient option and the first priority in most electrification strategies.
Utilities and other large fleets that view electrification through the lens of driving efficiency alone may miss a key opportunity to reduce their emissions. That’s because most work trucks are on the road for only a small portion of the day; their main purpose is to carry people and equipment to and from a job site. While the work is being done, they’re largely stationary.
For example, according to data from Ultimarc, the average heavy-duty bucket truck drives 9,283 miles per year (based on benchmark data from 2010-2014). That’s substantially less than other fleet vehicle categories.
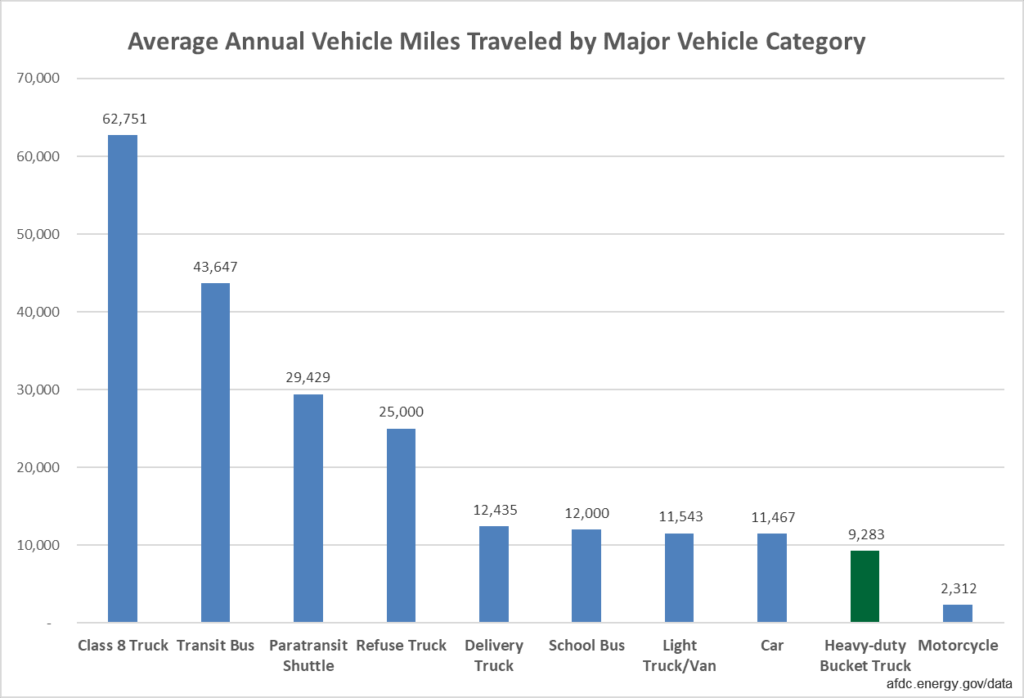
In other words, assets like bucket trucks are equipment first and vehicles second. In recent months, fleets have added the newly available all-electric options of work trucks, such as all-EV bucket trucks into their fleets. While these additions contribute significantly to the fleet’s electrification portfolio, there are opportunities to complement such all-electric acquisitions by considering the electrification (upfit or retrofit) of the work operations of the existing fleet.
If you’re only thinking about electrifying the entire truck, you’re missing a huge opportunity. You can complement purchases of newly available work vehicles like all-EV bucket trucks with electric upfits and retrofits of existing fleet assets. It’s a quick, easy way to increase efficiency and reduce emissions in parallel with larger acquisitions.
The key is to think of electrification from the equipment down to the vehicle, rather than from the vehicle up to the equipment. Approaching vehicles and the functions they perform as separate but complementary opportunities adds a huge amount of flexibility to your electrification plan.
Equipment-first is the smart, fast way to enhance fleet electrification
A vehicle-first approach demands a significant investment, likely requiring lengthy approval and procurement processes. If you lead with equipment, you may be able to start electrification immediately.
For instance, a utility with a fleet of several hundred diesel-fueled bucket trucks could upgrade these vehicles with electric Power take-off units (ePTOs) in a single day for a fraction of the cost of full EVs. In one fell swoop, this would electrify the work operation – and therefore the primary function – of its existing fleet assets. With every truck that is moved to the ‘electrified work operations’ column – whether via upfit, retrofit, or new EV purchase – the fleet gets closer to meeting its electrification, emissions, and cost reduction goals.
There are other benefits as well. Equipment electrification substantially reduces engine maintenance costs if you have trucks that mostly idle while working. Every hour a truck spends idling is equivalent to 30 driven miles – a 30 miles worth of wear and tear on the engine. Electrifying the work function reduces idling and enhances the life of the truck.
Leading utilities have shared other reasons for electrifying their work operations:
- While all-electric medium to heavy-duty work trucks are increasingly available, the options are still limited and supply chains are still catching up.
- Electrifying equipment is always cheaper than replacing an entire vehicle.
- Savings on fuel and maintenance are realized faster.
- The internal rate of return (IRR) is higher and the payback times are shorter, making it easier to meet utilities’ internal investment criteria.
- While there are hybrid solutions available in the market that are consistent with the old paradigm of the chassis powering the equipment, newer, more flexible technologies – namely electric power take-off units, or ePTOs – can readily electrify the equipment, separately from the chassis.
- Some of those existing solutions can be upfitted or retrofitted in a couple of days, rather than having to wait for months or potentially years to get a solution as part of a new truck.
- Some electric solutions are separate from the vehicle, so they:
- can operate separately from the truck, and you can switch operating modes from electric to chassis engine-driven when required.
- can be charged using a standard power outlet and don’t require a complex charging infrastructure.
- can be retrofitted and installed independently of the buying and selling cycles for work trucks.
- don’t impact the resale value of the truck as they can be removed before the sale; if anything, the resale value increases as the engine idles less in its lifetime.
Enhance your fleet’s electrification strategy by electrifying work functions!
There’s no doubt that fleet electrification is the way forward for utilities.
After all, the transportation sector contributes the largest portion of U.S. greenhouse gas emissions at 28 percent, according to the U.S. EPA., with the medium-and heavy-duty truck sector responsible for 23 percent of those emissions. And the policies that demand reduction in those numbers aren’t going anywhere.
It’s clear that beyond the obvious strategy of acquiring new all-electric vehicles, smart fleet managers should embrace technology solutions that electrify the large share of their fleet that spends more time idling than driving. Those who do can start electrifying their fleets sooner, less intrusively, and at a lower cost.
Wondering how much you could save with an equipment-plus fleet electrification strategy? Download our free idling calculator to see the numbers.
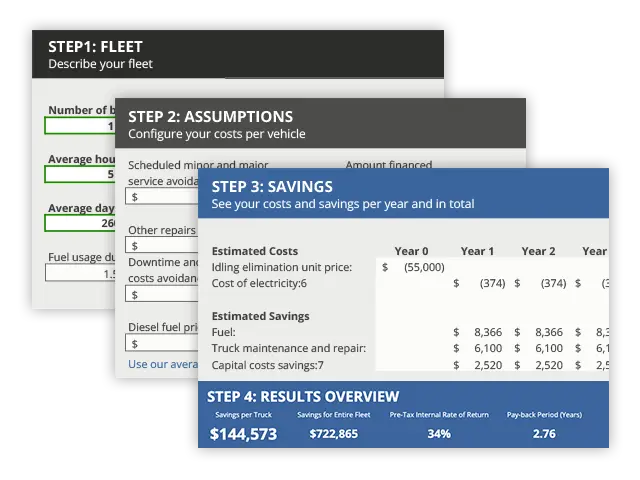