What is an ePTO?
ePTO, or electric power takeoff, is a technology that powers auxiliary functions on vehicles electrically, replacing traditional combustion engine methods. It offers benefits such as reduced emissions and cost savings.
How Does an ePTO work?
An ePTO works by harnessing electrical power from a battery or electric motor and transmitting it to auxiliary functions or equipment on vehicles. Instead of relying on a combustion engine for power, the ePTO utilizes electric power to operate various systems such as a hydraulic pump.
Key Components of ePTO Systems
The ePTO system consists of several key components. First, there is an electric power source, such as a battery or electric motor, that generates the necessary electrical energy. This power source is connected to an inverter or power electronics device, which converts the direct current (DC power) from the battery or motor into alternating current (AC) that can be used to power the auxiliary functions.
Next, the ePTO system includes a transmission mechanism, which transfers the electrical power to the desired application. This transmission mechanism can be in the form of a drive shaft, belt, or other mechanical linkage, depending on the specific requirements of the vehicle and the application.
Once the electrical power reaches the desired application, it can be used to power various auxiliary functions. For example, in a hybrid or electric vehicle, the ePTO can power systems such as air conditioning, heating, power steering, or even hydraulic systems for lifting and moving heavy loads.
The benefits of using an ePTO are numerous. Firstly, it reduces the reliance on a combustion engine, resulting in lower fuel consumption and emissions. This is particularly advantageous for companies looking to reduce their carbon footprint and promote sustainability.
What is a ePTO Used For?
Ground Zero: the Origins of Power Takeoff
the power take off has been around for a long time. Experimental versions were invented as early as 1878, while even before then there were other ways to transfer power from a running engine. Before the modern power takeoff, either the engine remained stationary, or the device only worked while the vehicle (in most cases a tractor) was actively moving, and was typically attached to the wheel. It was only until the first true power takeoff was invented, that we were able to proficiently utilize a drive train to operate equipment that didn’t slip, was easily connected and disconnected, and operated while the vehicle was making turns. It was these motivations that brought about the first ever commercial power takeoff.
The Journey of ePTO Development
Early PTO’s : The Beginnings

It wasn’t until 1918 when International Harvester Company (IHC) introduced the first commercial tractor power take off, the model 8-16, that they became a documented technology. Edward A. Johnston, and engineer for IHC, noticed the clever ingenuity of the farmers who had fashioned their own PTO’s in the hills of France and sought out to create a production model. After its release, it would only be another year before other competitors sprang up in a new race to satisfy consumers in the agricultural industry of the 1920’s. With that came the birth of the first generation of PTO’s.
Live PTO’s: Advancements in Power Takeoff
At this point a PTO’s installation in a transmission determined if the power takeoff could run independently of ground speed, or how fast the vehicle was traveling. Early on this was taken from the main output shaft, requiring the vehicle be in gear to operate. “Live” PTO’s were able to control the PTO’s rotation independently of the motion of the vehicle. This way the tractor could slow or stop while still running equipment. In 1945, Cockshutt Farm Equipment Ltd introduced the Cockshutt Model 30 tractor with LPTO and to this day the technology has remained fairly similar with most modern PTO’s considered to be “live.”
The Electric PTO (ePTO): A Revolution in Power Transmission
Oddly enough, the battery was invented before the PTO, but it wasn’t until decades later that people started attempting to electrify PTO’s for the sake of saving fuel. Once western culture became more environmentally aware in the early 90’s, ePTO’s finally started getting the attention they deserved, but the progression of batteries would serve to be an obstacle in their adoption.
First Generation vs. Modern ePTO: Comparing the Generations
It wasn’t long before people realized they could use battery power to operate PTO’s independently. In the early days of ePTO’s there was quite a bit of variety in architecture and battery chemistry. Most models weighed in at an unmanageable 1,500 lbs or more. They were also expensive with hefty price tags up to 100k and were largely unreliable. They had to be deeply integrated into the vehicle so much so that if the ePTO failed, the truck or tractor was put out of commission until the problem was resolved. This complicated a goal that was originally valid; improving the environment through emissions-reduction.
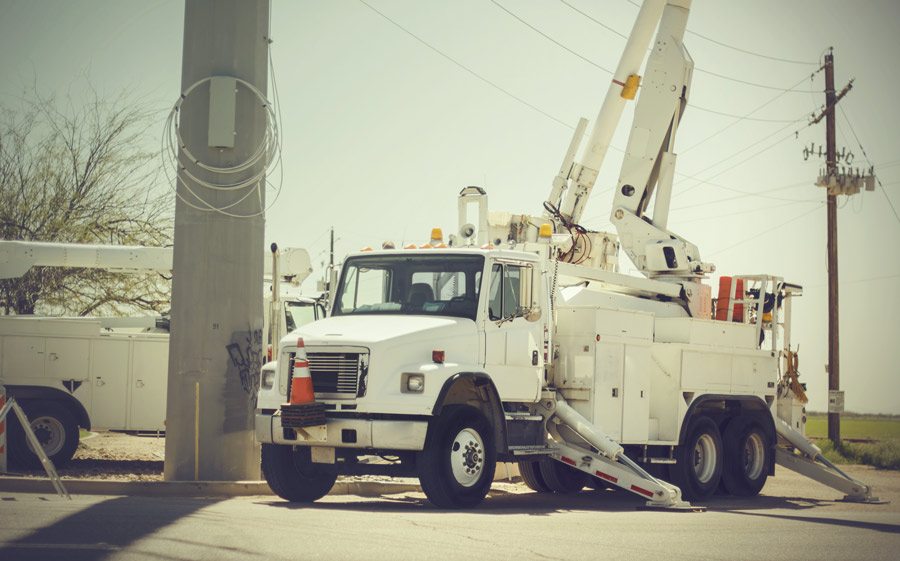
It was all too expensive to be worth the investment. Downtime related costs including repair, replacement vehicle, rentals, and loss of productivity could sometimes reach the initial unit cost of 60k or more, and the cost fell right in the customers lap. Most fleet managers shared negative experiences in this first rendition, experiencing hardware issues and fires along side lofty costs. Some companies were forced to close, evolve or sell those divisions to mitigate losses. All this was enough to leave a sour taste in the industry’s mouth despite the unit’s still being safer for crews and the environment.
ePTO’s had yet to really stick…
Second Generation of ePTO’s
After the turn of the millennium, concerns for climate change were mounting and generations of Americans were now old enough to bring it to the forefront of legislation and culture. By 2013 Lithium Iron Phosphate battery technology was allowing us to reevaluate the stability ePTO’s and the industry was cautiously ready to give them another shot. What came from this was a more reliable version of the utility. Though even such a short time ago, lithium batteries were still pretty heavy, and rather expensive, taking as long as 10 years for savings payback under reasonable total cost of ownership models, and the units were also still deeply integrated affecting resale value.
They also still risked taking your truck out of commission if they failed, averaging between $50,000 and $80,000 for a unit large enough to operate a bucket truck boom, bucket, or winch for a full workday. Annual fuel and maintenance savings (assuming no unexpected downtime) should have been around $4,500 to $9,500 annually, however, getting your money back on the investment still took longer than the average utility truck’s lifetime in a commercial setting. Although there was some improvement, it wasn’t sufficient to dispel the skepticism fleet managers had towards the product, stemming from their negative experiences with the first generation. The product was still lacking.
SmartPTO, Third Generation ePTO
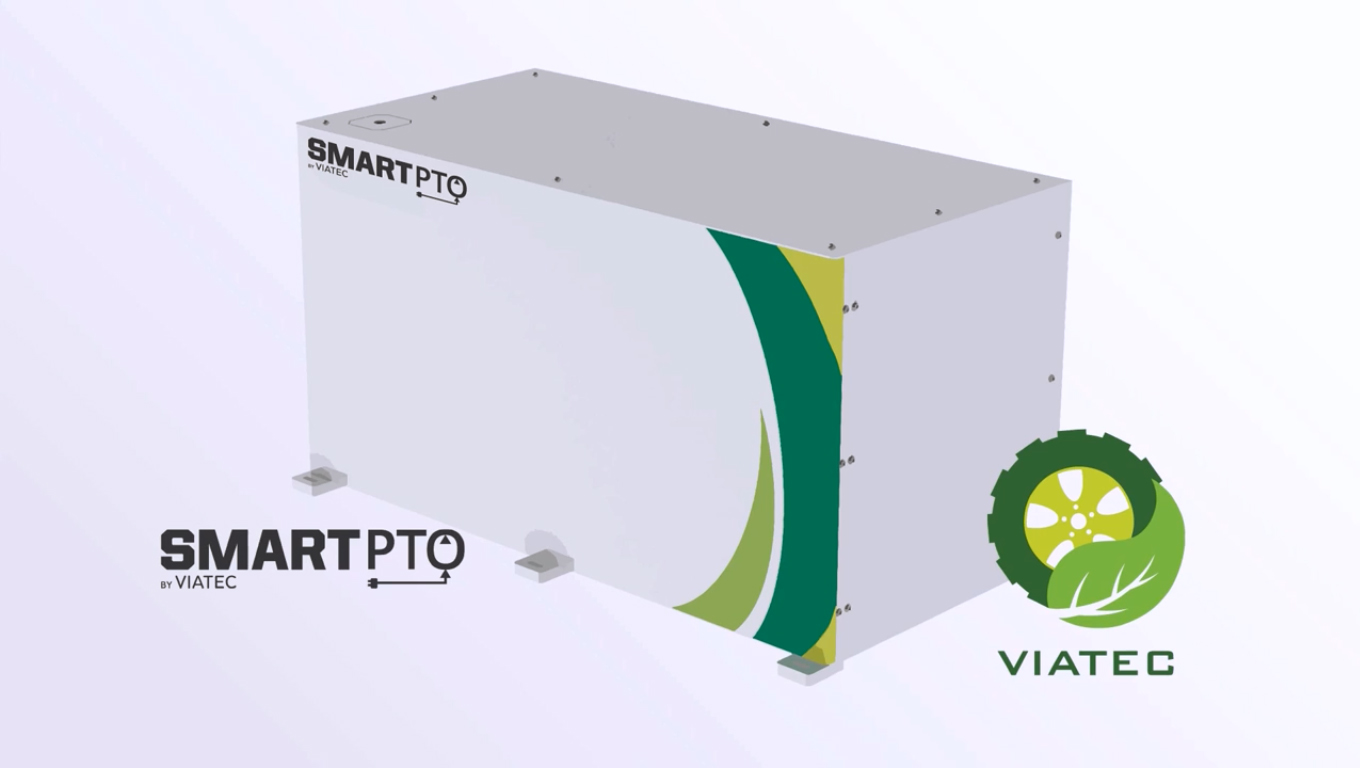
Today, the new generation of ePTO solves these problems. Like previous models, work can be done in a quieter, safer environment where ground crews can communicate freely. However, a key distinction nowadays is how modernized lithium batteries cost an average of $7,500 less and weigh significantly less. The unit weighs a grand total of 500 lbs on average.
Superiorly reliable, 3rd generation ePTO’s rarely fail and are truly parallel, meaning they can be deactivated to restore normal PTO use. They are easily transferable from one truck to another with a one to two day installation time.
Viatec’s Contributions to ePTO Advancements & Sustainable transportation
Rather than powering the drivetrain of the vehicle, SmartPTO by Viatec plugs directly into the hydraulic system, improving efficiency and making it easier than ever to retrofit existing fleets. This creates an average annual savings potential of up to $9,000, and a typical return on investment in less than 4-5 years.
Onboard telematics software allows for tracking, diagnosis, and raw data from the field, pushing updates and performance adjustments remotely. Most installations boast nearly $80,000+ in lifetime savings per system, and reduce maintenance costs by 69%.
So then, the special ingredient in calling an ePTO “3rd Gen” is its modular nature, and SmartPTO is the first of its kind. Developed by Viatec, it has a proven electric motor with over a decade of testing and two million dollars worth of research behind it.
Read to embrace the future of power takeoff technology? Discover how Viatec’s SmartPTO is is revolutionizing the industry with sustainable power for fleets. Learn more about our ePTO and electric fleet solutions.